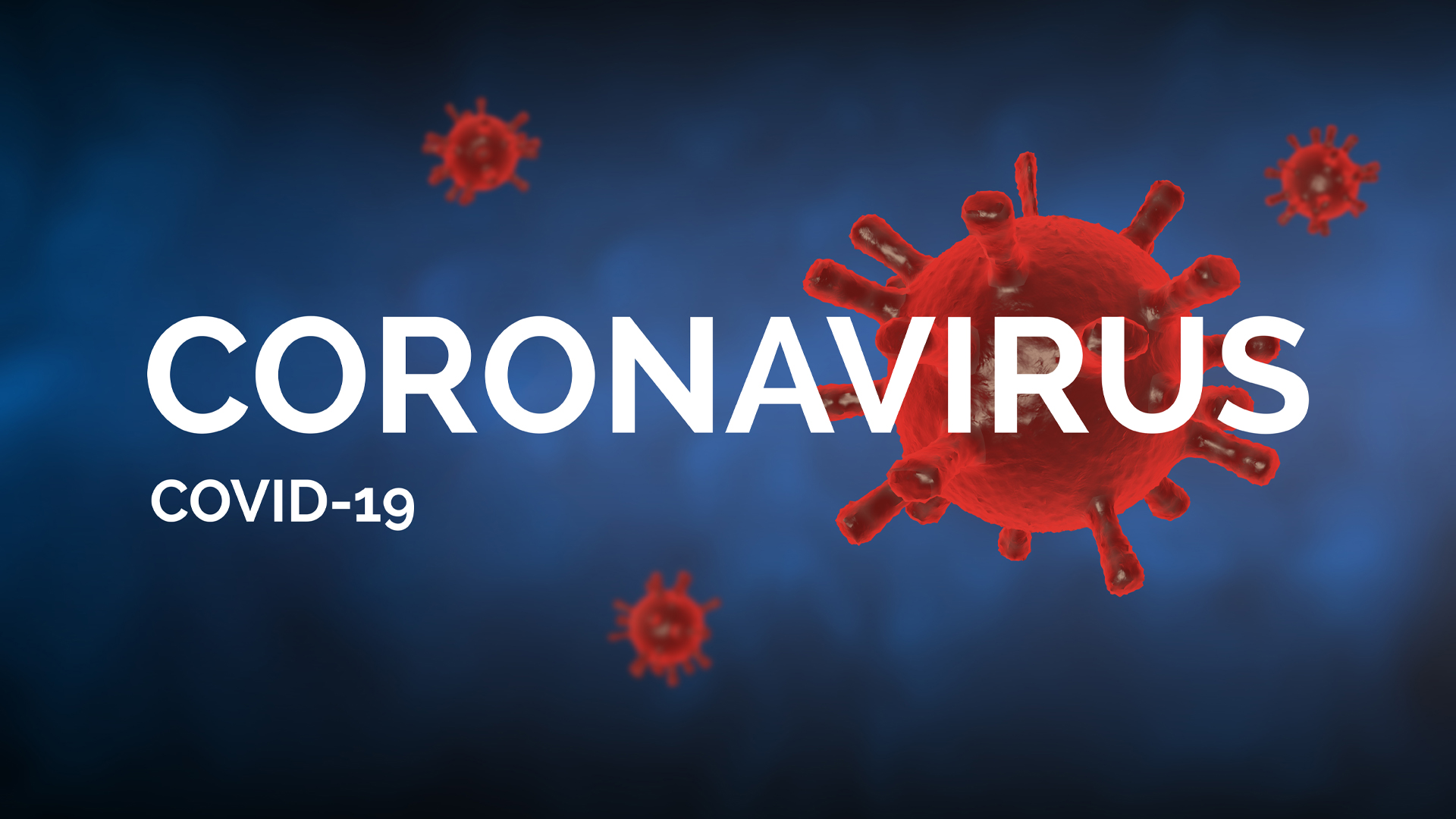
09 Apr OSHA Issues New Respirator Guidance
The Department of Labor’s Occupational Safety and Health Administration has issued new enforcement guidance on the use of respiratory protection equipment certified under international standards or other jurisdictions during the coronavirus disease pandemic. OSHA’s memorandum provides additional interim guidance to compliance safety and health officers for enforcing the Respiratory Protection standard (29 CFR § 1910.134) and certain other health standards, with regard to supply shortages of disposable N95 filtering face-piece respirators (FFRs).
All employers that have employees who are required to use, or are permitted to use respiratory protection voluntarily, must continue to manage their respiratory protection programs (RPPs) in accordance with the OSHA respirator standard. OSHA advises that they should also pay close attention to shortages of N95s throughout the COVID-19 pandemic and where possible, are encouraged to reassess their engineering controls, work practices and administrative controls to identify any changes they can make to decrease the need for N95 respirators. If respiratory protection must be used, and acceptable alternatives that are certified by the National Institute for Occupational Safety and Health (NIOSH) or ones that have exceeded their manufacturer’s shelf life are not available for use in accordance with OSHA’s April 3 memorandum, then employers may consider using respirators and filters certified under standards of other countries or jurisdictions.
OSHA advises that all employers should:
- Make a good-faith effort to provide workers with the most appropriate respiratory protection available for the hazards against which they need to be protected. This should be accomplished in this order:
- Implementing the hierarchy of controls in an effort to first eliminate or reduce workplace hazards, then using engineering controls, administrative controls and safe workplace practices to prevent worker exposures to respiratory hazards.
- Prioritizing efforts to acquire and use equipment in the following order:
- NIOSH-certified equipment;
- Equipment certified in accordance with standards of other countries or jurisdictions, except the People’s Republic of China, unless equipment certified in accordance with the standards of the People’s Republic of China is manufactured by a NIOSH certificate holder;
- Equipment certified in accordance with the standards of the People’s Republic of China, the manufacturer of which is not a NIOSH certificate holder; and
- Facemasks (e.g., medical masks, procedure masks).
- Prioritizing efforts to acquire and use equipment that has not exceeded its manufacturer’s recommended shelf life before allowing workers to use expired equipment. Equipment used beyond its manufacturer’s recommended shelf life must be used in accordance with OSHA’s April 3 memorandum.
- Prioritizing efforts to use equipment that has not exceeded its intended service life (e.g., disposable FFRs used for the first time) before implementing protocols for the extended use or reuse of equipment. The extended use or reuse of equipment should follow the Centers for Disease Control and Prevention’s Strategies for Optimizing the Supply of N95 Respirators.
- Using homemade masks or improvised mouth and nose covers only, as a last resort (i.e., when no respirators or facemasks are available). Improvised masks are not personal protective equipment and ideally should be used with a face shield to cover the front and sides of the face. When this measure is the only resort, refer to the CDC’s guidance.
- Ensure employees know how to perform a user seal check each time they wear a respirator, regardless of whether it is a NIOSH-certified device or device certified under standards of other countries or jurisdictions. Do not allow employees to use a respirator on which they cannot perform a successful user seal check (See 29 CFR § 1910.134, Appendix B-1, User Seal Check Procedures).
- Train workers on how to visually inspect FFRs to determine if the structural or functional integrity of the respirator has been compromised. Over time, components, such as the straps, nose bridge and nose foam material, may degrade, which can affect the quality of the fit and seal. Workers must understand that if the structural or functional integrity of any part of the respirator is compromised, to protect their health and safety, it should be discarded.
- Avoid co-mingling products from different categories of equipment. For example, NIOSH-certified equipment, equipment that was previously NIOSH-certified but has surpassed its manufacturer’s recommended shelf life, equipment certified under standards of other countries or jurisdictions and equipment that was previously certified under standards of other countries or jurisdictions but has surpassed its manufacturer’s recommended shelf life, should be stored separately.
Train employees on the procedures for the sequence of donning/doffing to prevent self-contamination.